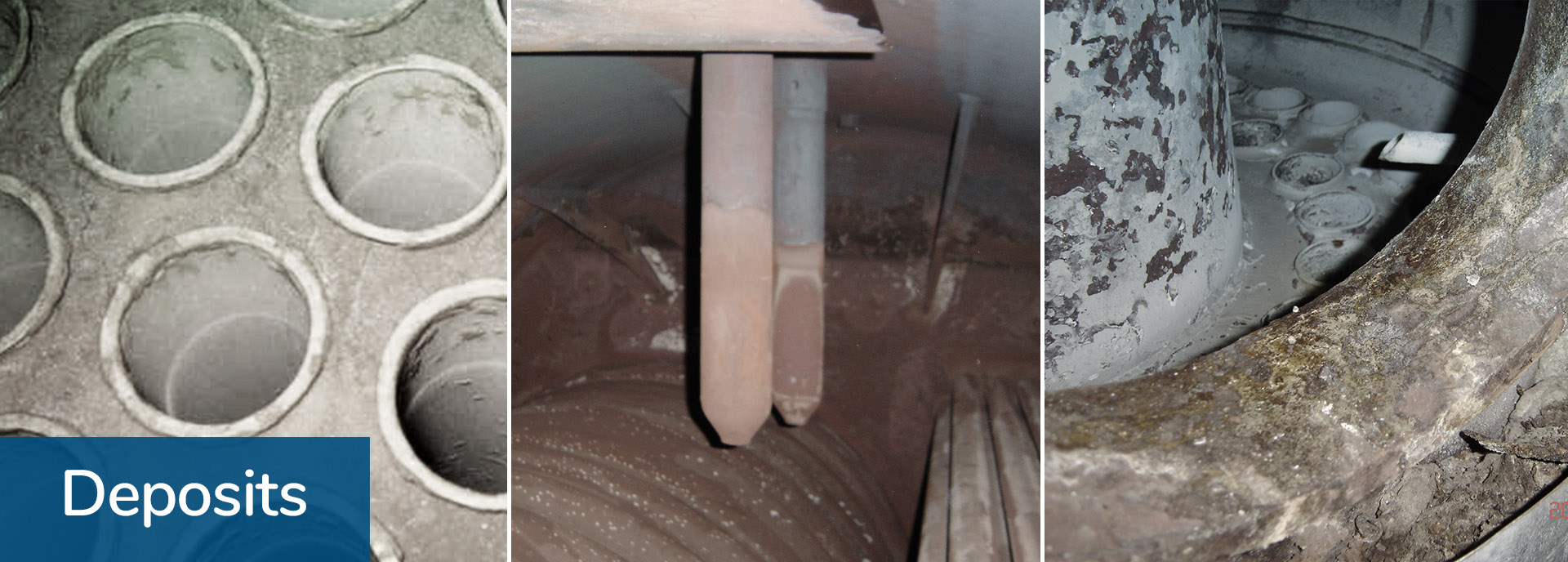
Formation and prevention of scales
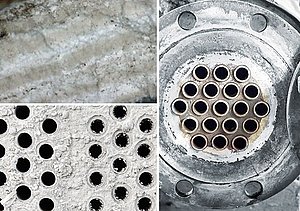
The formation of scales can be favored by various factors, such as chemical reactions, temperature, pressure and solubilities of the substances involved, such as water, produced food, etc.
There are different types of scales that can vary depending on the industry and the specific conditions. Some of the most common types are:
- Calcium deposits: They are formed by the crystallization of calcium and magnesium salts from hard water. Scale buildup can occur in piping, heat exchangers, and other equipment, reducing flow rates and affecting efficiency.
- Rust and corrosive layers: This type of scaling occurs on metal surfaces when they come into contact with moisture and oxygen. Rust can affect the integrity of metal structures and cause serious damage.
- Organic deposits: They can consist of organic compounds such as oils, fats, proteins or other biological materials.
- Biofilms: These are complex combinations of microorganisms that colonize surfaces and form a protective layer there. These can be stubborn and difficult to remove.
Various measures can be taken to prevent or reduce scales in the industry:
- Regular cleaning and maintenance: Regular cleaning of equipment and surfaces can help minimize the formation of scales.
- Use of additives: In some cases, special additives can be introduced into the production process to prevent or reduce the formation of deposits and scales.
- Control of process parameters: Controlling process parameters such as temperature, pressure and pH can help reduce the formation of scales.
- Descaling and rust removal: In some cases, it is necessary to perform regular descaling and rust removal procedures to remove any deposits that have already formed.
- Use of filtration and separation techniques: The use of filtration and separation techniques can remove impurities from liquids and gases, minimizing the formation of scales.
In the following presentations, we focus mainly on the different types of lime scale in sugar factories. We provide an overview of scales, focusing on beet sugar / beet sugar factories, but also highlight aspects specific to cane sugar production. In the case of scales in the sugar industry, it is primarily lime scales that occur.
Scaling
When water is heated, the dissolved minerals it contains can crystallize and deposit as scale on the inside surfaces of boilers, piping and heat exchangers. Scale formation can affect the efficiency of heating systems and steam boilers, as the deposits hinder heat transfer and increase energy costs.
In the case of lime deposits, the term "scale" – also referred to as boiler scale – is often used.It is a typical scale that occurs in steam boilers and heating systems. It is a solid deposit of lime that forms when hard water, with a high content of calcium and magnesium salts, is heated.
In addition, scale deposits can promote corrosion, shortening equipment life.
The composition of the scale is analyzed using a combination of specific modified methods, including:
- ICP-OES (inductively coupled plasma – optical emission spectrometry)
- Ion Chromatography–
- Titration methods
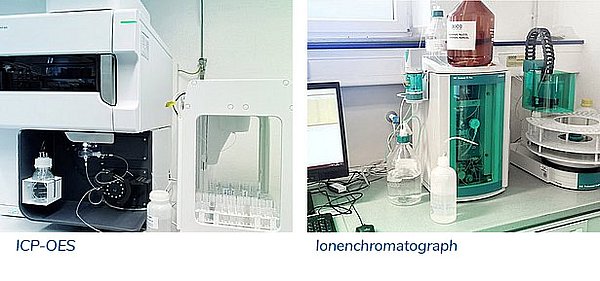
KEBO has analyzed over 10,000 scale samples collected over a period of more than 40 years from over 1,000 factories in approximately 60 countries.
In addition to some process changes that reduce the formation of a particular type of scale, there are two main techniques for scale prevention:
- the use of ion exchange resins to replace calcium with sodium or hydrogen cations, and
- the use of antiscalants to stabilize the scale-forming compounds in a microcrystalline state
In the following illustrations we show the main lime scales that are common to the sugar industry.
The main components of scale
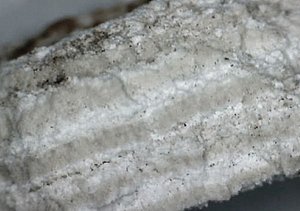
The main scale constituents are calcium salts, silicates and sometimes sugar carbon. Other inorganic scale constituents are of minor importance or rather special scenarios. In addition to the chemical composition, the removal of scale is influenced by its structure. Scale built up from layers (see figure) is often more difficult to remove and may require repeated chemical treatment.
Calcium oxalate
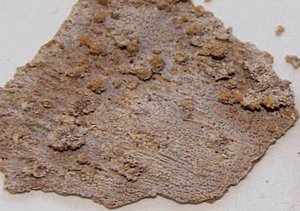
Calcium oxalate occurs in beet and cane sugar factories and is formed in the crops by various reactions from precursor substances. It remains the most important scale constituent in the sugar industry and limits uptime if the juice is not treated. Calcium oxalate-containing scales exhibit a wide variation of colors and structures. Examples are shown in Figures 2 and 3.
Calcium oxalate is not soluble in alkaline or acidic cleaning solutions, so cleaning in two steps is required. In the first, alkaline step, the oxalate is converted to calcium carbonate by sodium carbonate being added in excess to the alkaline cleaning solution.
Dispersants and wetting agents are added to the cleaning solution to improve its penetration into the scale and to achieve a complete conversion reaction not only on the surface of the scale.
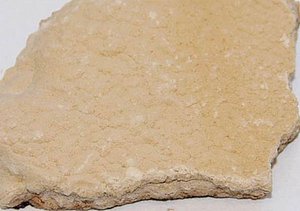
In the second, acidic step, the calcium carbonate formed is dissolved with an acid containing a corrosion inhibitor to protect the system.
In practice, formic, sulfamic or hydrochloric acid are used. The formation of calcium oxalate deposits is no longer considered a problem in the European sugar industry, as their formation can be well prevented by thin juice softening, the use of polyacrylate-based antiscalant, or a combination of both techniques.
Calcium carbonate
Calcium carbonate is formed in sugar factories during "carbonation" in heat exchangers for limed/carbonated juice as a result of the addition of milk of lime or saccharate and CO2. Sometimes calcium carbonate is also found in evaporator stations, indicating a need for optimization in the carbonation process, such as improving reaction times or filtration.
Reduced use of lime and further optimization of juice purification in the European sugar industry, however, are reducing the importance of calcium carbonate as a boiler scale component.
Scales, whose composition is predominantly calcium carbonate, can be removed by dissolving with inhibited acid. The formation and precipitation of calcium carbonate is the desired reaction during carbonation. In the evaporator stations or in further process steps, the formation can be prevented by optimizing the carbonation, e.g. by softening the thin juice or applying polyacrylate-based antiscalant.
Calcium sulfate and calcium sulfite
Calcium sulfate or calcium sulfite is occasionally found in the scales of "sulphation" sugar factories. It results from the excess addition of SO2 or (bi-)sulfite. In some areas, high sulfate content in sugar cane results in calcium sulfate scales even without sulphation. For the cane sugar industry, this type of scale is of increasing importance as the trend is towards the production of low-color raw sugar and plantation white sugar.
For the removal of calcium sulfite or sulfate scales, conversion with sodium carbonate – as described above for oxalate – is recommended, since sulfite forms gaseous SO2 when treated directly with acid.
Calcium phosphate
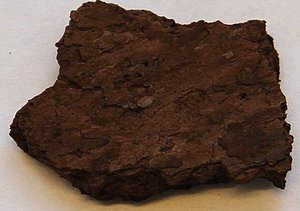
Calcium phosphate is the main compound that occurs in cane sugar factories in the initial stage and limits their operation time. It can be removed by acid cleaning with inhibited formic or hydrochloric acid. Most calcium phosphate enters the evaporators as particles rather than as dissolved ions. Calcium-phosphate-containing scales often have a less dense but thick structure (Fig. 5) and a dark color, indicating that they have originated from sludge particles rather than from crystallization of ions. Therefore, the most effective prevention is the optimization of the juice purification process, especially in sedimentation and filtration. Calcium phosphate scales, which are later formed by crystallization, can be prevented by using polyacrylate-based antiscalant.
Calcium aconitate
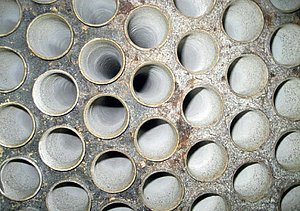
Calcium aconitate is one of the essential scale types in South America. If the juice is not treated, it can cause significant operational problems with late effects.
Calcium aconite scales are very difficult to remove, especially mechanically. They can be easily removed chemically with formic acid and an inhibitor. Calcium aconitate formation can be prevented through the use of polyacrylate-based antiscalants.
Calcium citrate
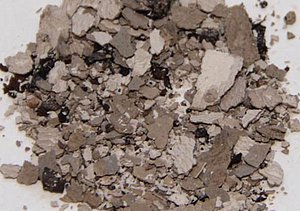
When citric acid is used to chemically clean evaporators, calcium citrate scale can form because the soluble calcium citrate complex known from low-temperature cleaning applications is not stable at high temperatures. Therefore, citric acid is not recommended for cleaning evaporators at high temperatures.
Silicates
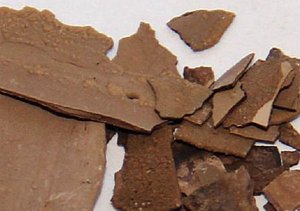
Silicates are found in beet and cane sugar factories. While silicates in the cane sugar industry come from sugar cane, the main source of silicates in the beet sugar industry is limestone. In scale, silicate is usually not present as simple silicate. Silicates in scale have complex polymer structures and often occur as aluminum, magnesium and calcium silicates, especially in beet sugar factories.
- Prevention: The silicate content increases with decreasing pH at the point of use, therefore: do not use fresh milk of lime for second carbonation.
- Prevention for cane sugar factories: Use of polyacrylate-based antiscalant
Sugar charcoal and caramelized sugar
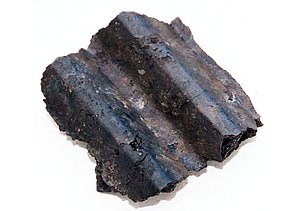
Sugar charcoal and caramelized sugar are formed when sugar is burned on hot surfaces. This often happens as an accident during a power interruption or other unexpected malfunction. This type of encrustation shows an increasing tendency, mainly because the risk of accidents increases with the duration of the campaign. Outages caused by internal and external problems with power grids are being reported from a growing number of factories. In addition, the success of falling film and plate evaporators in the sugar industry has increased the risk for such scales, as these types of evaporators are more susceptible to the formation of sugar charcoal in the event of a failure (Fig.).
If the pipes or the space between the plates are not completely clogged, the sugar charcoal can be removed with an alkaline solution containing suspending agents and wetting agents. The suspending agent is important because the solution often removes the scale from the surface, but does not dissolve it 100%. Modern evaporators have an emergency system for water supply in the event of a malfunction to avoid the formation of sugar carbon. In cases where sugar caramelizes during standard operation, optimizing the juice distribution of the juice distribution system can reduce the problem.
Antiscalants
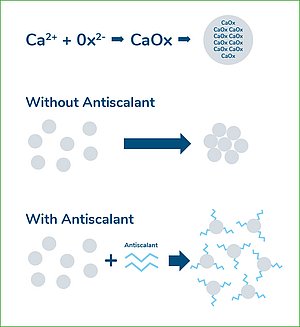
Antiscalants for use in sugar juice are based on polyacrylate, and this chemical is restricted by national and international regulations. A polyacrylate-based antiscalant prevents scale formation by stabilizing small, still invisible microcrystals of calcium salts that form as the juice evaporates and concentrates. Without antiscalant, the microcrystals grow, stick together and form scale in this way. The antiscalant is able to attach one end of its molecular chain to the surface of the microcrystals and prevent them from growing further. As a result, the microcrystals remain stable in the juice, so that from a technical point of view they behave as if they were still in solution.
The products shown on our website are only a selection of our entire product range. There is no universal remedy for the rapid removal of impurities. Some can be removed well with alkaline agents, others better in the acidic range. The large variety of conceivable cleaning problems and the large number of additives, inhibitors and ready-to-use cleaning solutions offered by us make it advisable to obtain detailed advice before starting cleaning.
The same applies to inhibitors, defoamers, scale preventers, corrosion inhibitors, pickling inhibitors, etc. Depending on the plant, material, product and the type of boiler/cooling water is used, different individual challenges arise. We are well equipped for them.
Talk to us, we will be happy to help!
On request, we can analyze deposits in our laboratory and develop a cleaning strategy based on our many years of experience, taking into account the conditions on site.