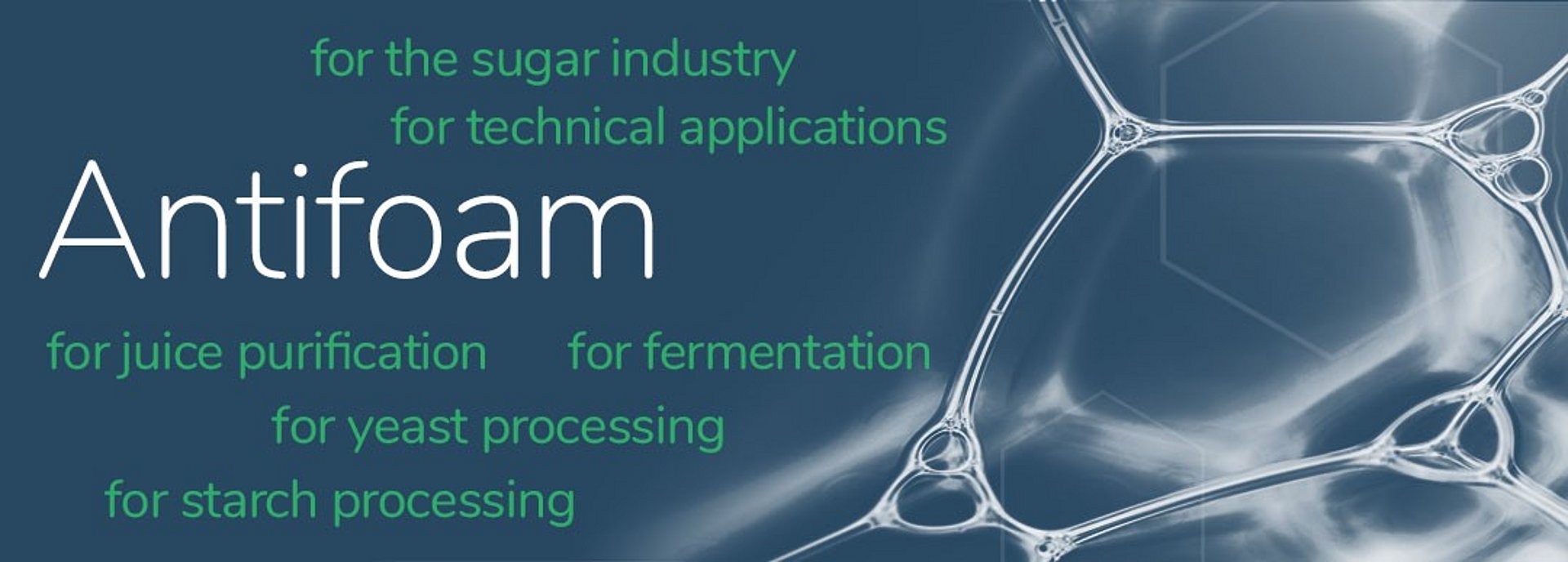
Versatile solutions for foam control in industrial processes: KEBOSPUM
In almost all industrial production processes, unwanted foam formation can occur. This foaming can affect process efficiency and lead to disruptions in operations and significant losses in production volumes. To prevent this and maximize productivity, defoamers are used.
Foaming agents include saponins, proteins, glycosides from sugar- and starch-containing plants, metabolites from wastewater treatment, and surfactants.
Our highly effective defoamers are specially developed either to eliminate foam immediately as defoamers (spontaneous action) or to prevent its formation from the outset as antifoams. In both cases, the long-term effect is to suppress (renewed) foam formation.
Our defoamers meet a wide range of requirements and can be used in various applications. They not only support process stability, but also optimize the quality of the end products by preventing contamination and other negative effects. At the same time, they do not negatively affect the individual process steps and ensure smooth production.
The surface-active substances effectively prevent the formation of foam during fermentation and distillation of preparations from fruit, grain, starch, potatoes, sugar.
From the mechanisms of surface-active processes, it can be explained that defoamers of certain types can develop maximum effectiveness only in certain temperature ranges. For interior applications, our products have been formulated for the temperature range of 40 °C and higher.
Here now is a small insight into the many possible applications:
Defoamer for the sugar industry – for interior and exterior use
KEBO supplies defoamers for internal operation in beet and cane sugar factories and for the alluvial water area in beet sugar factories. Due to their special formulation, they have the property of spreading instantaneously in the medium to be defoamed, and of settling just as quickly in the interfaces that are formed, in order to displace foaming substances such as saponins, proteins, etc. present therein. The defoamers for interior operation exhibit equal foam-destroying power in all liquids.
Effective defoamers for optimized juice extraction
In juice extraction, the control of foaming is an important aspect to ensure smooth production processes and high quality juices. Our defoamers provide customized solutions for the juice industry to efficiently reduce unwanted foam, whether for sugar juices during clarification in carbonated lime, during evaporation or for fruit pulp press waters.
Our defoamers are stable and maintain their effectiveness over time. They are resistant to juice production conditions, such as pH, temperature and pressure, and ensure reliable foam control.
Defoamers for starch processing
In starch production, various processes are carried out to extract starch from vegetable raw materials such as corn, potatoes or wheat.
The main process steps are usually the digestion reaction, the separation of starch from other components such as proteins and fibers, and the drying of the extracted starch.
Digestion involves dissolving the starch in water and then heating it to open the starch granules and break up the starch structure. Foaming can occur during this process, which can affect the efficiency of digestion.
Defoamers in starch production are added to the digestion water to reduce surface tension and thus control foaming.
Defoamers for yeast processing
A silicone-free antifoaming agent designed for foam control in a variety of processes. It consists of plant-based alkoxylated fatty acid esters and is free of mineral oils.
During yeast production, various processes are carried out to propagate and harvest yeast in large quantities. The most important process steps in yeast production are usually yeast propagation, harvesting of the yeast, and processing and storage of the extracted yeast.
Defoamers are used in yeast production during the fermentation process. Yeast fermentation takes place in a tank where the yeast is provided with nutrient media and oxygen to multiply and produce alcohol. During this process, foaming can occur, which can affect the efficiency of the fermentation.
The defoamers in yeast production have the task of reducing the resulting foam. They are added to the fermentation medium to reduce surface tension and thus control foam formation.
Defoamers help break down foam and prevent it from rising excessively and interfering with the fermentation process.
Defoamers for fermentation
In fermentation, organic substances are transformed by the metabolism of microorganisms such as bacteria, yeast or fungi. There are several types of fermentation used in different industries, including food and beverage, biotechnology, and chemistry. Defoamers are used in various fermentation processes.
Here are some examples:
- Brewing beer: Yeast is used in beer production to enable the conversion of sugar into alcohol. During fermentation in the fermenters may occur foaming, which can affect the efficiency of fermentation.
- Winemaking: In winemaking, fermentation is carried out by yeast, which converts the sugar in the grape juice into alcohol. Here, too, foam can develop during fermentation, which is undesirable. Defoamers are used to control the foam and ensure good mixing of the fermentation medium.
- Fermentation of dairy products: In the production of yogurt, cheese and other fermented dairy products, specific cultures of lactic acid bacteria are used to enable fermentation. Foam may also occur here, which can affect the quality and efficiency of fermentation.
Defoamers for technical application
In technical applications, there are a variety of processes where defoamers can be used.
Here are some examples:
- Industrial cleaning: When cleaning surfaces or industrial equipment, cleaning agents can generate foam. Defoamers are used to control foam and allow efficient cleaning. They must reduce foam quickly, with low residue to ensure thorough cleaning.
- Paper manufacturing: In the paper industry, a mixture of water, fibers and chemical additives is used during paper production. This mixture may cause foaming, especially during dewatering and processing of the paper. Defoamers are used to reduce foam and improve the quality of the paper.
- Oil and gas industry: In the oil and gas industry, foaming can occur during the extraction, processing and storage of oil and gas. This can affect the efficiency of the processes and cause problems. Defoamers are used to control foam and optimize equipment performance.
- Wastewater treatment: During the treatment of wastewater, certain chemical reactions or bacterial cultures can produce foam. Defoamers are used to reduce foam and improve the efficiency of wastewater treatment. They must be able to effectively control foam while being environmentally sound.
The products shown on our website are only a selection of our entire product range. There is no universal remedy for the rapid removal of impurities. Some can be removed well with alkaline agents, others better in the acidic range. The large variety of conceivable cleaning problems and the large number of additives, inhibitors and ready-to-use cleaning solutions offered by us make it advisable to obtain detailed advice before starting cleaning.
The same applies to inhibitors, defoamers, scale preventers, corrosion inhibitors, pickling inhibitors, etc. Depending on the plant, material, product and the type of boiler/cooling water is used, different individual challenges arise. We are well equipped for them.
Talk to us, we will be happy to help!
On request, we can analyze deposits in our laboratory and develop a cleaning strategy based on our many years of experience, taking into account the conditions on site.